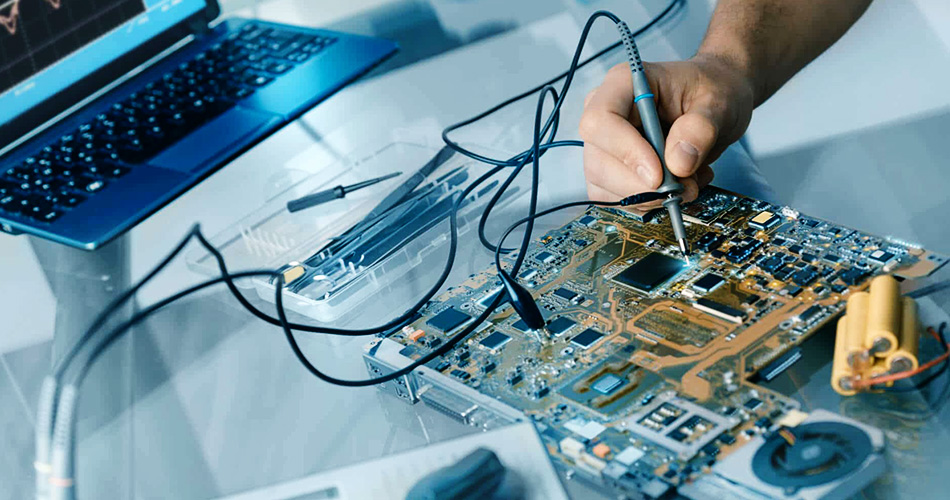
在PCBA(印刷电路板组件)的制造和测试过程中,尽管采用了先进的工艺和严格的质量控制,但仍难以完全避免测试失败的情况发生。当一块PCBA未能通过功能或电气测试时,它通常需要经过故障诊断、返工修复,然后再次进行测试,即返工与重测(Rework & Retest)。如何高效、准确地处理这些返工与重测板,是提升生产直通率、控制成本、确保产品最终品质的关键环节。测试失败的源头往往可以追溯到PCBA加工过程,因此理解并管理好这一环节至关重要。
PCBA测试失败的原因多种多样,了解这些原因有助于更有效地处理问题:
1、PCBA加工缺陷:这是最常见且直接导致测试失败的原因之一。例如,锡膏印刷不良导致的虚焊、连锡;元器件贴装偏移或极性错误;焊接温度曲线不当引起的焊点问题;或清洗不彻底造成的残留物短路等,这些都直接反映了PCBA加工过程中的质量控制水平。
2、元器件本身缺陷:采购的电子元器件可能存在批次性问题、参数漂移或早期失效。
3、设计或PCB缺陷:电路设计错误、布局不当,或者PCB裸板制造过程中存在问题(如线路断裂、层间短路、过孔问题)。
4、测试环节问题:测试程序错误、测试夹具故障、探针接触不良、测试设备校准失效等,可能导致误判(假失败)。
明确故障原因,特别是区分是PCBA加工问题、元器件问题还是设计问题,是进行正确返工和采取预防措施的基础。
当一块PCB板测试失败后,规范的处理流程通常包括以下几个步骤:
1、故障定位与诊断:根据测试报告提供的故障信息,结合电路原理图、PCB布线图,使用万用表、示波器、逻辑分析仪等工具,精确定位故障发生的位置和原因。这一步需要有经验的测试或维修工程师执行。
2、故障记录:详细记录失效的PCBA板号、测试工位、失败的项目、故障现象以及诊断出的具体原因和位置。这些记录是后续进行数据分析和过程改进的重要依据。
3、返工操作:由经过专业培训的返工技术人员,使用恰当的工具(如热风枪、烙铁、吸锡器、返修台等)和符合标准的返工规范,对故障点进行修复。返工操作需要极其精细,尤其是对于细间距、BGA等元器件,避免对周边器件或PCB造成二次损伤。返工本身可视作一种特殊的PCBA加工行为,其质量同样关键。
4、返工质量检查:返工完成后,需要对返修区域进行严格检查,通常会使用放大镜、显微镜,对关键焊点甚至需要进行X射线检查,确认修复效果,并检查是否引入了新的缺陷(如焊盘翘起、新增的连锡)。
5、重测:将返工后的PCBA重新送回测试工位进行测试。至少需要重新测试之前失败的项目,通常建议进行完整的最终测试,以确保故障已被彻底排除,并且返工操作没有引入新的问题。
6、记录与追踪:在PCBA的生产追溯系统中更新返工和重测的状态、结果以及相关的维修记录。
仅仅遵循返工流程是不够的,提升返工效率和减少需要重测的板子数量,需要更积极主动的策略:
1、源头控制:大幅提高PCBA加工质量。 最根本、最有效的策略是减少测试失败的发生。这意味着要从源头抓起,严格控制PCBA加工过程的每一个环节:优化锡膏印刷工艺、提高贴片精度、设定合理的焊接温度曲线、确保清洗质量。通过在PCBA加工完成后的早期阶段就进行SPI、AOI、X射线等检测,尽早发现并修正缺陷,可以显著降低流入功能测试环节的不良品率。
2、投资精准的故障定位工具和培训。 快速准确地诊断问题可以缩短返工时间。投入先进的测试设备和诊断工具,并持续对测试及维修人员进行技术培训,提升其故障分析和返修能力。
3、规范化返工流程与强化技能培训。 建立清晰、可操作的返工指导书,并确保返工人员掌握针对不同类型元器件和缺陷的正确返修技巧,避免二次损伤和重复返工。
4、优化测试方案与信息输出。 设计能够提供更详细故障信息的测试程序,例如直接指示短路点的位置或具体失败的元器件,可以极大地提高诊断效率。
5、建立数据分析与闭环改进机制。 定期分析测试失败的数据,找出高发的失败类型、原因(特别是与PCBA加工相关的缺陷),并将分析结果反馈给设计、工程和PCBA加工团队,推动工艺改进和设计优化,从根本上减少问题的重复发生。
6、设定合理的返工次数限制。 过度的返工可能会对PCBA的可靠性造成损害,应根据产品类型和可靠性要求,设定单块PCBA允许的最大返工次数。
PCBA测试中的返工与重测是制造过程中的常态,但并非不可管理。高效处理的关键在于建立规范的流程,并更重要的是,采取积极措施减少失败的发生。其中,大幅提高PCBA加工的质量水平是降低返工率和重测率的最有效手段。结合精准的故障诊断、专业的返工技能、以及基于数据分析的持续改进,企业能够有效管理返工与重测问题,最终提升产品良率,降低制造成本,并确保交付给客户的PCBA具备高可靠性。