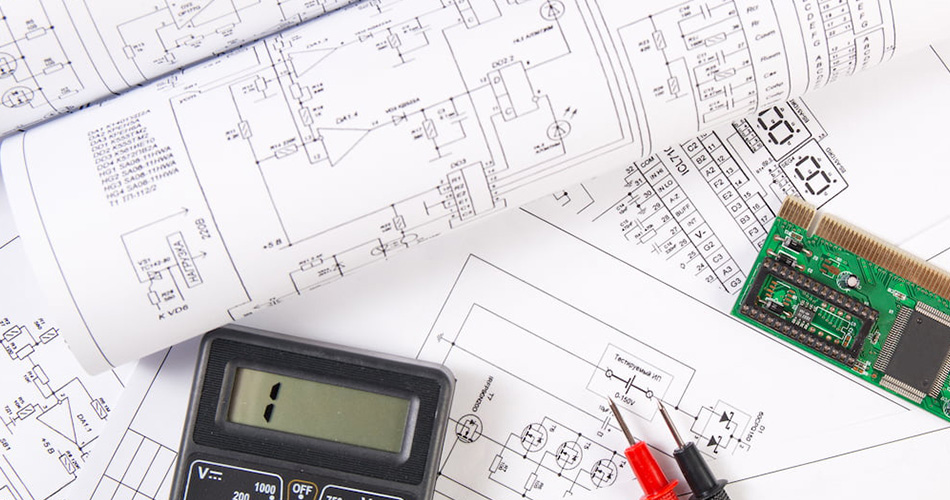
PCBA(印刷电路板组件)测试是电子产品制造流程中不可或缺的一环,用于验证产品的功能和可靠性。然而,测试往往是成本和时间的主要消耗点,尤其当测试过程中出现大量问题时,不仅拉长了生产周期,也增加了返工和维修的成本。许多测试中发现的问题并非测试本身造成,而是源于更早期的阶段——特别是PCBA的设计。通过在设计阶段进行优化,可以显著减少下游测试环节的问题,提高整体效率。本文将探讨PCBA测试中常见的设计相关问题,并分析如何通过优化设计、特别是加强可测试性设计(DFT),与PCBA加工紧密配合,从而减少测试难题。
PCBA测试中令人头疼的问题,很多都可以在设计阶段找到根源:
1、测试点不足或位置不当:这是最常见的设计问题之一。测试点过少或分布在难以接触的位置(如元器件下方),使得自动测试设备(如ICT、飞针测试仪)无法有效地探测到关键电路节点,导致测试覆盖率低或无法定位故障。
2、关键信号或电源节点未引出:在进行功能测试或故障诊断时,如果关键的信号线、电源线或控制线没有在板边、连接器或测试点处引出,工程师将难以监测信号波形、电压或电流,给调试带来极大困难。
3、电路设计不易测试:某些电路设计过于复杂,缺乏简单的初始化或复位机制,内部状态难以控制或观察,使得测试程序编写复杂,且难以验证所有工作模式。
4、元器件布局不利于测试:元器件之间距离过近,阻碍测试探针的下压;大型元器件遮挡了周围的测试点或小型元器件,影响测试和返工。不合理的布局也可能增加PCBA加工的难度,导致焊接缺陷。
5、未考虑测试模式或内置测试功能:设计中没有加入方便测试的逻辑或接口,例如边界扫描链(Boundary Scan)未正确连接,或者没有预留用于进入测试模式的跳线或引脚。
6、信号完整性或电源完整性问题:设计时未充分考虑高速信号的阻抗匹配、串扰或电源网络的压降、噪声等问题,这些设计缺陷可能导致PCBA在功能测试中出现间歇性故障或性能不达标,且问题难以诊断。
7、与PCBA加工工艺不兼容:设计采用了超出常规PCBA加工能力的元器件封装(如超细间距BGA)、特殊的板材要求或复杂的叠层结构,增加了PCBA加工的难度,容易产生虚焊、连锡、板层缺陷等问题,这些缺陷最终会在测试中暴露。
为了从源头减少PCBA测试中的问题,设计阶段应重点关注可测试性设计(DFT – Design for Testability)并兼顾可制造性设计(DFM – Design for Manufacturability):
1、强化可测试性设计(DFT):
- 合理、充分地设置测试点:在外层为关键信号节点、元器件引脚、电源和地平面设置足量的、符合间距和尺寸规范的测试点,确保ICT和飞针测试的覆盖率。
- 利用测试接入点:在板边或合适位置预留测试连接器或排针,方便功能测试和调试设备的连接。
- 集成边界扫描等内置测试功能:对于数字电路比例高、集成度高的PCBA,采用支持边界扫描的芯片,并在设计中正确实现边界扫描链,可以在无需大量物理测试点的情况下,有效测试芯片间的互连。
- 设计易于控制和观察的电路:在设计中加入测试使能信号、内部节点监测点或简化的测试模式,方便在测试时隔离和验证电路功能。
- 考虑测试模式:设计简单的跳线或软件指令,使PCBA能够进入特定的测试模式,简化测试程序。
2、兼顾可制造性设计(DFM):
- 与PCBA加工团队紧密协作:在设计评审阶段就引入PCBA加工工程师的意见,了解其工艺能力限制。
- 选择易于加工的元器件和封装:尽量避免使用过于特殊或对PCBA加工要求极高的元器件,确保元器件的可靠贴装和焊接。
- 遵循合理的布局和布线规则:确保元器件之间、焊盘之间的距离满足PCBA加工的要求,减少连锡、虚焊等风险,也方便测试探针下压。
- 设计符合PCBA加工能力的板层和过孔结构。
- 一个易于PCBA加工的设计,其产生制造缺陷的概率会大大降低,从而减少测试发现的缺陷数量。
3、提升设计质量的其他方面:
- 进行信号完整性/电源完整性仿真:在设计阶段通过仿真工具预先评估和优化高速信号线和电源网络的质量,从源头避免功能测试中可能出现的性能问题。
- 提供清晰、完整的文档:详细的原理图、PCB文件、BOM清单和设计说明,有助于测试工程师理解电路,高效开发测试方案和进行故障诊断。
成功的PCBA产品离不开设计、PCBA加工和测试环节的紧密协同。设计师不仅要关注电路功能实现,还需要深入了解PCBA加工工艺能力和测试方法的原理与局限性。测试阶段发现的问题(无论是PCBA加工缺陷还是设计缺陷),应及时准确地反馈给设计和PCBA加工团队,形成改进闭环。可测试性设计(DFT)和可制造性设计(DFM)不是设计工程师单方面的任务,而是需要设计、工艺、测试等多部门共同评审和决策的协同成果。
减少PCBA测试中的问题,最根本且有效的方式是在设计阶段进行优化。通过贯彻可测试性设计(DFT),合理设置测试点、利用边界扫描等技术,并兼顾可制造性设计(DFM),与PCBA加工能力相匹配,可以显著提升PCBA的可测试性。加强设计、PCBA加工和测试团队之间的沟通与协作,利用测试反馈持续改进,是从源头控制问题、提高测试效率、加速产品上市、并最终交付高质量产品的关键保障。