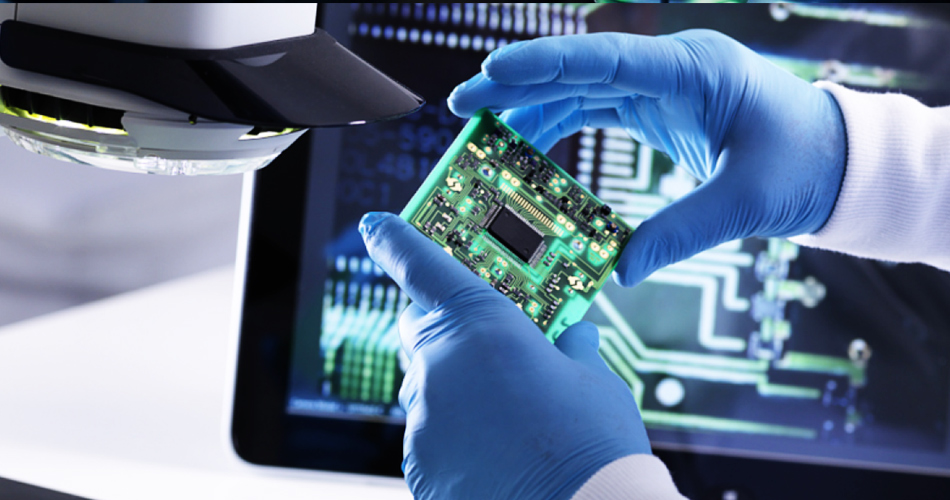
随着电子产品功能的不断提升,PCBA加工中的电路板也愈发复杂,多层板、高密度元器件、BGA封装等设计已成为常态。这类复杂电路板对测试的覆盖率和准确性提出了更高要求,测试完整性直接影响产品的出厂品质和后续稳定性。要想在PCBA加工中确保复杂板卡的测试完整性,需要在设计、工艺、设备和管理等多个层面协同发力。
1. 从设计阶段就考虑可测试性
测试完整性的前提,是电路本身具备良好的可测试性。在产品研发阶段,应引入DFT(Design for Testability)理念,合理规划测试点数量和分布位置,确保后续ICT或FCT测试能够全面覆盖关键电路。
尤其是在高密度布线或空间受限的设计中,要提前与PCBA加工厂进行协同评审,避免因设计限制导致关键节点无法测试。对使用BGA、QFN等封装的芯片,更应考虑是否需要预留辅助测试通道或采用边界扫描方式进行补充测试。
2. 采用多种测试手段组合验证
在复杂电路板的PCBA加工中,单一测试手段往往无法满足全覆盖需求。通常需要将ICT、FCT、AOI、X-Ray等多种测试方式结合使用:
- ICT在线测试:适合检测开短路、电阻电容值等静态参数,适用于覆盖基础连接问题;
- FCT功能测试:通过加载程序或模拟使用场景,验证板卡的逻辑、通信、控制功能是否正常;
- AOI自动光学检测:快速识别焊点虚焊、偏移、极性错误等外观缺陷;
- X-Ray检测:用于检查BGA等不可见焊点,弥补目检和AOI的盲区。
通过交叉测试,能够提高整体测试的准确率和覆盖率,确保即便单一环节出现疏漏,也能在其他测试中被及时发现。
3. 确保测试程序与治具的专业性
复杂PCBA的功能测试通常需要定制测试治具与测试程序,这部分的专业性直接决定了测试完整性的水平。测试治具需要覆盖所有需接触测试的点位,并具备稳定的结构设计和防呆机制,避免误操作。
测试程序方面,应根据不同模块功能进行模块化编写,逐一验证通信接口、电源、传感器输入输出、芯片响应等功能点。对关键参数应设定合理的判定阈值,并具备错误提示和数据记录功能,确保每次测试都有据可查。
4. 建立测试结果的数据追溯体系
复杂电路板的测试数据量大,必须依靠系统化管理进行存储与追溯。建议引入MES系统或自动测试记录平台,实现测试数据与产品序列号的绑定。
在后续出现客户反馈或质量问题时,可快速调取历史测试记录,帮助溯源分析、定位问题。同时,积累的数据也可用于优化测试策略,提高整体测试效率和准确率。
5. 组织跨部门联合评审与持续优化
PCBA加工涉及设计、工艺、测试、品控等多个环节。对复杂电路板的测试策略,应定期组织联合评审,分析缺陷出现的阶段与分布,及时调整测试流程和测试覆盖点。
同时,结合良率数据与客户反馈,对测试流程进行持续改进,有效减少测试盲区和误判率,进一步提升产品的综合竞争力。
确保复杂电路板中的PCBA测试完整性,并非依赖某一项技术或单一设备,而是需要设计合理、测试手段丰富、治具专业、数据可控、流程持续优化的系统化配合。只有在整个PCBA加工链条中建立起高标准的测试理念,才能真正做到高可靠、高一致性的产品交付。