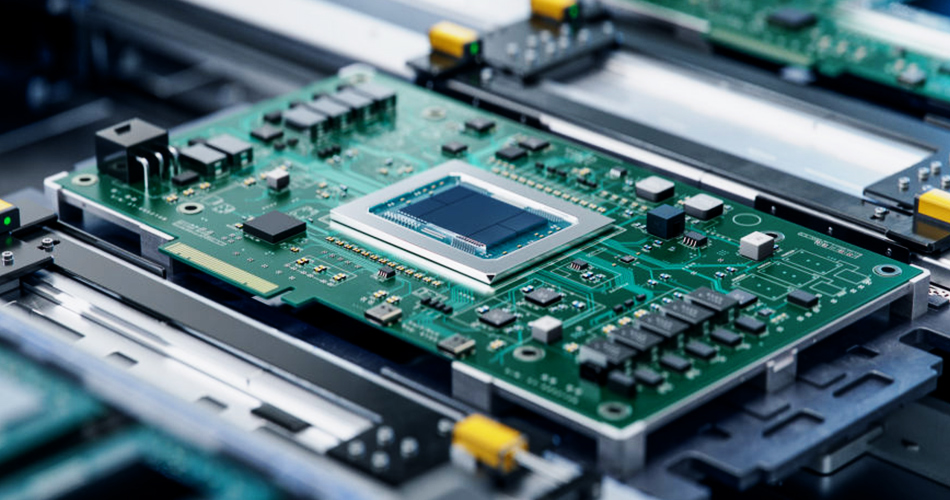
随着电子产品向小型化、高功能、高密度方向发展,PCBA加工所涉及的电路板结构也越来越复杂。传统的测试方式已难以满足这些高度集成产品的质量验证需求。因此,开发一套量身定制的测试方案,成为保障PCBA加工品质的关键。以下从实际生产需求出发,探讨如何为高度集成的电子产品设计出高效、可执行的PCBA测试方案。
1. 从产品结构和功能出发制定测试策略
高度集成的产品往往集成多个模块,如射频、MCU主控、通信接口、电源管理等,每个模块对测试的要求不同。测试方案应以产品功能为核心,根据模块划分测试单元,并制定相应的测试项目和优先级。
例如:
- 射频部分需测试发射频率、功率稳定性;
- 通信模块需验证接口连通性和协议响应;
- 电源模块则需测试稳压输出与过载保护等。
只有理解整板的系统逻辑,才能设计出覆盖率高、逻辑清晰的测试流程。
2. 提前介入设计阶段,落实可测试性原则
在PCBA加工中,“可测试性设计”(DFT, Design for Testability)是定制测试方案的基础。设计阶段若未预留足够测试点或测试接口,后续测试将陷入被动,甚至无法全面验证。
建议在PCB布线前,就与测试工程师联合评审,重点关注以下几点:
- 是否为关键信号预留测试通道;
- BGA、QFN等芯片是否具备边界扫描支持或替代测试方案;
- 是否可通过程序下载口进行在线功能验证;
- 是否考虑未来维护或固件升级所需的测试接口。
通过前期介入,既能降低测试难度,也能提高整线良率。
3. 选用合适的测试方式组合
高度集成产品的测试通常无法依赖单一手段完成。常见的组合方式包括:
- ICT(在线测试):检测元件值、短路、开路等基本电气特性;
- FCT(功能测试):通电后模拟实际工作场景,测试整板功能表现;
- 边界扫描测试(JTAG):用于复杂封装的信号链路验证;
- 自动光学检测(AOI)与X-Ray:检测外观焊接质量与隐藏焊点。
测试方式的选择需结合产品特性、成本预算和批量大小灵活配置,目标是在不影响产能的前提下,最大限度提升测试覆盖率。
4. 定制高匹配度的测试工装和程序
标准测试治具往往难以适配高度集成的非标产品,建议根据实际板型和结构定制测试工装,包括:
- 高精度测试夹具:保障接触点稳定,避免误判;
- 模块化插针结构:方便维护和更换;
- 软件定制测试程序:涵盖各模块输入输出、协议识别、电气指标判断、测试日志记录等功能。
测试程序应支持快速更新和批次切换,适配产品可能存在的功能迭代。
5. 加强测试数据分析与结果追溯
定制测试方案不仅关注“能不能测”,更要关注“测了以后能否解释和追溯”。建议接入MES系统,实现每块PCBA的测试数据、测试工位、操作人员、测试日志的绑定,便于后续质量分析和问题溯源。
对于量产产品,可定期通过SPC(统计过程控制)分析测试数据波动,优化测试阈值,提升测试效率和良率。
在PCBA加工过程中,标准化固然重要,但面对高度集成的电子产品,唯有因产品而异地制定测试方案,才能实现真正的质量保障。从设计介入、测试方式选择,到测试工装定制与数据管理,整个过程需各部门协同推进。一个科学、高效的定制测试方案,不仅是对产品品质的保障,也是加工厂核心竞争力的重要体现。