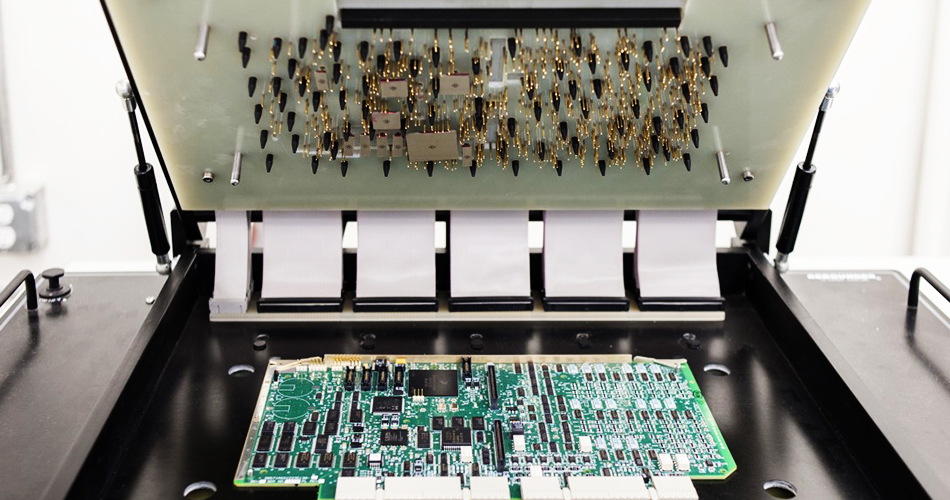
在电子产品日益复杂、客户需求高度差异化的背景下,PCBA加工企业越来越多地面临“定制化测试”的要求。相比标准化流程,测试定制需要在方案设计、软硬件匹配、工艺实施等多个层面进行深入配合。如何在效率、成本和品质之间找到平衡,已成为摆在PCBA加工厂面前的重要课题。
1. 功能复杂性带来的测试覆盖难题
随着产品集成度提升,一块PCBA可能承担多个系统级功能,如电源管理、信号处理、通信交互等。面对这种多模块、跨协议、异构接口的结构,传统的单一测试手段显然无法实现有效覆盖。
解决方案:
加工厂应在前期深入参与客户方案评审,协助明确测试边界和重点功能。测试平台方面,可构建“通用控制器+专用功能板”的组合架构,支持灵活切换测试逻辑。测试程序设计上,引入模块化结构,根据客户产品特性快速拼接测试流程,既保证覆盖率,又提高开发效率。
2. 小批量、多批次带来的治具经济性挑战
在定制项目中,客户往往采用小批量试产或多型号并行开发,这对测试治具的通用性和成本控制提出更高要求。若每个项目都需重新开发专用夹具,不仅投入高,还极易造成资源浪费。
解决方案:
优质PCBA加工厂应具备“模块化夹具平台”设计能力。即在一个通用底座基础上,通过更换探针板、定位模块等快速适配不同板型,减少重复制造成本。同时,可结合二维码识别自动切换测试参数,实现多型号共用测试平台。此外,在条件允许的前提下,可建议客户在设计阶段预留标准测试点,降低后续夹具定制难度。
3. 测试数据管理与追溯的系统化难点
定制化测试往往涉及多个工位、多个步骤,如何确保测试过程可控、结果可查、异常可追,是对加工厂信息化能力的直接考验。特别是在医疗、汽车等高可靠性行业,客户对数据完整性和可追溯性要求极为严格。
解决方案:
建议PCBA加工厂引入MES系统或自建测试数据平台,对每块板卡的测试过程进行实时记录与统一管理。每块PCBA绑定唯一条码,所有测试数据自动归档至数据库,并生成电子报告,可供客户远程查阅或导出归档。对于测试异常的记录,应实现闭环处理机制,并支持按SN码回溯历史操作行为,提高问题定位效率。
定制化测试已成为PCBA加工服务的重要组成部分,它不仅检验加工厂的技术实力,也直接影响产品出厂品质与客户信任。面对功能复杂、批次多变、数据可控等挑战,唯有通过标准化的定制流程、模块化的测试平台和系统化的数据管理,才能在满足客户个性化需求的同时,实现效率与品质的双重保障。