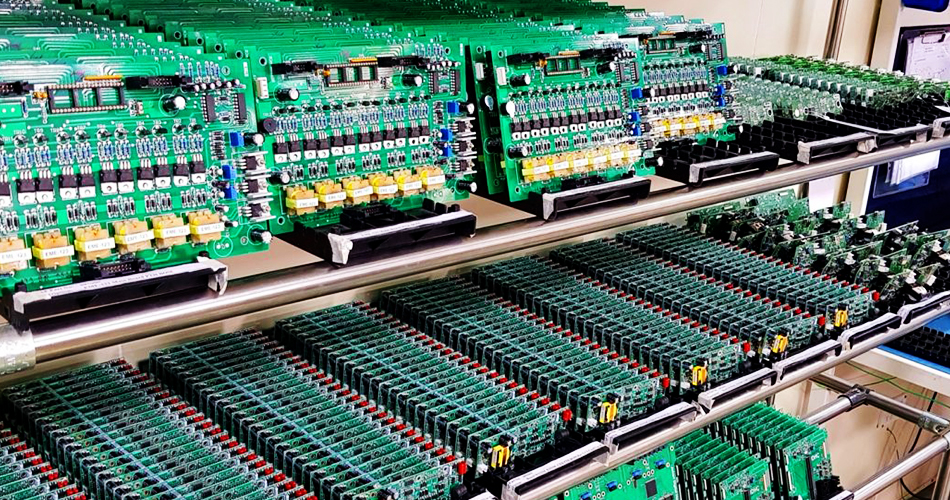
在电子制造行业,PCBA加工的整体成本受多方面因素影响,包括材料、人工、设备折旧、测试流程等。其中,测试环节既是保障产品品质的重要步骤,也往往是影响交付周期与制造成本的关键因素之一。如何在确保品质的同时,通过更高效的测试手段降低成本,已成为许多PCBA加工企业关注的重点。
1. 测试流程设计直接影响生产节奏
在PCBA加工中,测试流程是否合理,直接决定了整条产线的节拍效率。测试工位若设计不当,容易形成瓶颈,导致前后工序等待,增加无效工时。
为避免此类问题,应在产品导入初期就参与测试方案的规划,提前考虑:
- 是否具备可并行操作的模块化测试流程;
- 测试夹具是否便于快速定位与切换;
- 工站安排是否合理分布,避免单点测试时间过长。
通过流程优化,不仅可以提高产能利用率,还能减少不必要的等待与搬运成本。
2. 提前介入设计阶段,减少后期返工
许多测试难题并非出现在测试本身,而是源于前期缺乏“可测试性设计”(DFT, Design for Testability)的考量。例如:
- 没有预留足够的测试点;
- 接口信号难以激活;
- 模拟电路无法在板上完成有效验证。
这类设计问题一旦进入批量阶段,往往只能通过加装飞线、局部修改来补救,既增加返工成本,也影响整体交付节奏。为避免此类情况,建议PCBA加工厂在打样阶段与客户密切沟通,协助其完善设计方案,从源头上提升测试效率。
3. 自动化测试降低人工与误判率
在传统FCT(功能测试)过程中,人工判断依赖经验,容易造成漏测或误测,影响品质稳定性,也带来重复测试或误返的成本。引入自动化测试平台,可显著提升测试效率与一致性:
- 自动判定电压、电流、通讯协议等信号是否合格;
- 系统记录每块板的测试数据,便于后期追溯;
- 测试程序可统一维护、快速升级,减少人力投入。
在大批量生产项目中,自动化测试所节省的工时和避免的误工返修,可显著降低单位成本。
4. 夹具标准化与模块化,节省开发投入
定制测试夹具是PCBA加工中的一项重要投入,尤其在小批量、多批次项目中,若每个产品都单独开发,成本高、周期长。为此,建议采用模块化、标准化夹具平台:
- 通用底板+可更换测试模块的结构设计;
- 通用针床接口,兼容不同尺寸PCB;
- 可视化操作界面,降低操作门槛。
通过批量使用标准件,既降低了材料与设计成本,又缩短了开发周期,提升整体项目响应速度。
5. 建立测试数据系统化管理机制
测试数据的系统化管理不仅有助于品质控制,更能在返工处理、客户对账、异常分析中提供依据,减少人为沟通成本。建议在PCBA加工过程中建立以下机制:
- 每块板唯一编号与测试数据绑定;
- 系统自动生成测试报告,支持导出归档;
- 测试异常自动拦截并记录处理结果。
这些措施将帮助企业在控制质量的同时,压缩不必要的返工、沟通及重复测试带来的成本支出。
高效测试不仅是保障PCBA加工品质的手段,更是优化制造成本结构的关键环节。通过前期介入设计、优化测试流程、引入自动化手段与夹具标准化管理,PCBA加工企业可以在保证产品可靠性的前提下,大幅降低制造过程中因测试带来的隐性成本。测试做得好,成本自然低,这已成为行业内越来越多企业的共识。