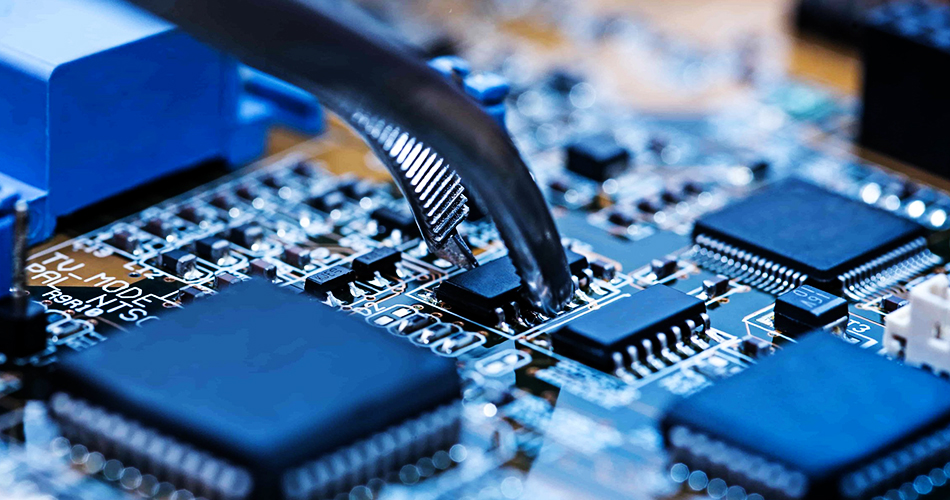
在PCBA加工过程中,测试环节是确保产品质量的重要保障。但与此同时,测试也往往是整个制造流程中耗时耗工、成本占比较高的一部分。如何在不牺牲检测质量的前提下,通过流程优化来降低测试成本,是每一家电子制造企业都关心的问题。
通过对测试流程的系统性优化,不仅可以有效控制成本,还能提升生产效率和产品良率。以下几个方面,是实现测试成本优化的关键切入点。
1. 测试方案前置,避免重复投入
许多PCBA加工企业在客户提供设计方案后才开始规划测试流程,往往容易出现测试点不足、接口不合理、夹具复杂等问题,最终导致返工、修改甚至二次开发测试工装,从而大幅增加测试成本。
解决办法是在产品设计早期阶段,即介入DFT(Design for Testability)设计评审,提前识别可能影响测试效率的结构问题。比如:
- 预留统一的测试点布局
- 简化信号采集路径
- 规划标准化的测试接口
测试方案的前置介入,有助于从源头降低测试难度与后期返工率。
2. 合理划分测试流程,提升测试效率
PCBA加工中的测试流程通常包括ICT(在线测试)、FCT(功能测试)、老化测试等。将不同测试环节科学分工,有助于降低整体测试时间和设备占用率。
优化策略包括:
- 将基础的电气性开短路检测集中于ICT完成,快速筛除重大不良;
- 将软件加载与功能验证集中于FCT,流程统一、脚本自动化;
- 对高稳定性要求的产品实施抽检老化测试,降低全检成本。
通过分阶段的测试策略安排,可有效减少冗余测试与资源重复使用,提高人均测试效率。
3. 夹具与测试平台的模块化设计
测试夹具的开发通常是成本控制的重点之一。为不同项目反复开发夹具,不仅周期长、费用高,也不利于后期维护。
应推广通用化、模块化的夹具平台设计:
- 采用统一底板结构,不同产品更换上盖模块即可测试;
- 共享测试主控系统和功能接口板,减少重复开发;
- 易于维护与升级,延长设备生命周期。
在中小批量、多品种的PCBA加工项目中,模块化夹具方案具有更高的成本回收效率。
4. 自动化测试系统减少人力投入
传统人工测试存在判断误差大、效率低、数据不可追溯等问题,导致返修率上升,间接增加测试与售后成本。引入自动化测试系统可显著改善这些问题:
- 自动加载程序、激活功能、判断结果,减少人工干预
- 测试数据自动记录与上传,便于后期追踪分析
- 支持远程维护和脚本更新,缩短停线调整时间
尽管自动化测试设备前期投资较高,但其在长期使用过程中对测试效率和一致性控制的提升,可显著摊薄单位成本,形成良好的投资回报。
5. 搭建数据追溯系统,减少重复检测
测试过程中若缺乏统一的数据平台,容易出现重复测试、结果缺失、问题难定位等情况,增加无形成本。建议建立完善的测试数据追溯系统:
- 每块PCBA绑定唯一编号,记录完整测试流程
- 异常板自动隔离,避免流入下工序造成更大损耗
- 分析测试趋势,提前预警工艺问题,防止批量不良
通过数据系统的建设,不仅可以提升产品质量管控能力,也能显著降低重复检测、误判导致的资源浪费。
PCBA测试不只是发现问题的工具,更是控制成本、提升效率的关键环节。通过优化测试流程、提高自动化水平、推进夹具通用化、建立数据闭环管理体系,PCBA加工企业能够在保证质量的前提下,实现测试成本的有效控制。在行业竞争日益激烈的今天,谁能在测试环节做到高效、精准、低耗,谁就能在制造成本上赢得更大的优势。